Production facilities
Omnic Factory
At Omnic, we firmly believe that in-house production is a key to ensure the highest level of product quality, while maintaining employee well-being, social responsibilities and environmental-friendly production methods.
.webp)
Production Facilities
We control every stage of equipment production, from initial R&D to launched parcel locker business, all performed by our team of experienced specialists.



Total area of production facilities
Production capacity of modules annually
Professionals involved in the production process
Electricity from renewable energy sources
Our Certificates
All OMNIC products comply with European quality and safety standards as well as national standards (Georgia and Turkey). The components we use are CE EU and RoHS certified, which guarantees compliance with European safety and environmental standards.
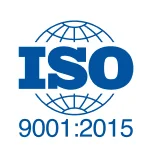
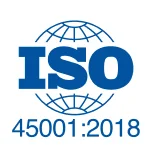
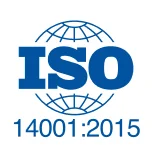
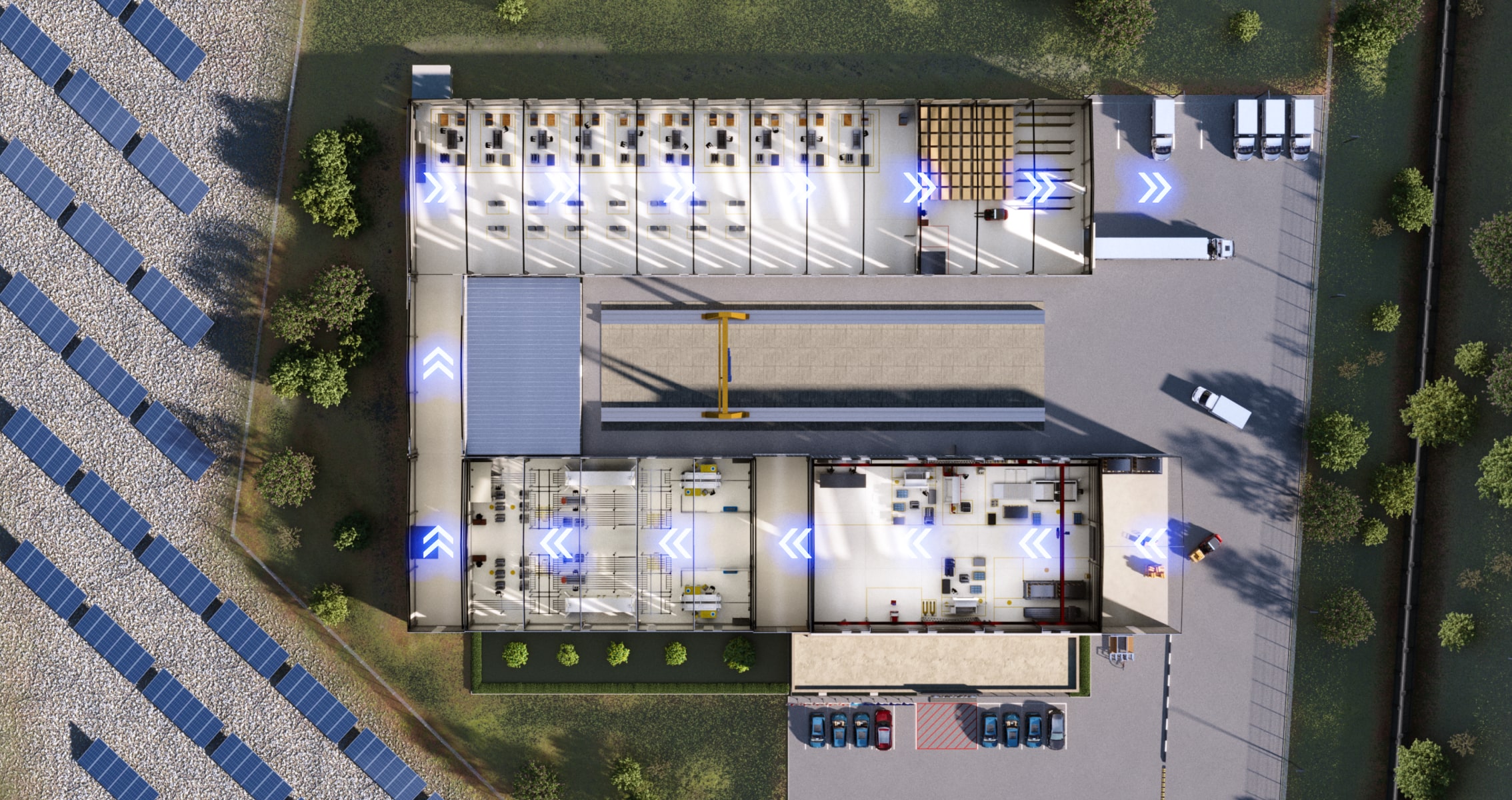
Our Production Process
We have 5 levels of quality control at each stage of production to ensure the Exceptional quality
01
Design and Engineering
The production process begins with the design and engineering phase, where the concept and specifications of a parcel locker are developed. Our Hardware R&D team operates in two main areas: developing parcel lockers and self-service solutions, and creating custom products upon client request. The team consists of Product Managers, Design Engineers, Embedded Developers, and Researchers.
02
Material Procurement
Once the design is finalized, the necessary materials for constructing the parcel locker are procured. This may include metals, plastics, electronic components, and other required hardware.
03
Manufacturing
He manufacturing phase involves fabricating the different components of the parcel locker. This includes cutting and shaping metal or plastic sheets, welding or joining the components, and assembling them to form the locker structure.
04
Installation of Electronic Components
In this step, electronic components such as sensors, control panels, and locking mechanisms are installed into the locker. Wiring and connections are established to ensure proper functionality.
05
Testing and Quality Control
After the assembly is complete, thorough testing is conducted to ensure that the locker functions correctly. This includes checking the electronic systems, locking mechanisms, and overall durability of the locker. Any necessary adjustments or improvements are made during this stage.
06
Branding and Packaging
Once a parcel locker passes the quality control tests, it undergoes finishing processes such as painting, coating, or applying any required branding or labeling. Parcel lockers are then carefully packaged to protect them during transportation and storage.
Pioneering a Greener Future in Manufacturing
OMNIC Factory is 100% carbon-free. Our solar infrastructure generates 0.5 MW of energy, providing enough electricity for manufacturing.
FAQ
What types of products are manufactured at OMNIC Factory?
OMNIC Factory is focused at advanced self-service solutions only. Our state-of-the-art facility is equipped to handle everything from design and engineering to final assembly and quality control, ensuring high-quality, reliable products.
What certifications does OMNIC Factory hold?
OMNIC Factory is certified with ISO 9001:2015 for Quality Management Systems, ISO 14001:2015 for Environmental Management Systems, and ISO 45001:2018 for Occupational Health and Safety Management Systems. These certifications demonstrate our commitment to maintaining the highest standards in quality, environmental responsibility, and workplace safety.
How sustainable is the OMNIC Factory?
OMNIC Factory is dedicated to sustainability and operates on 100% solar power. Our facilities are designed to minimize environmental impact, and we continuously seek ways to improve our processes to promote a greener future in manufacturing. Visit OMNIC Green Factory to learn more.
Can OMNIC Factory handle custom manufacturing requests?
At OMNIC Factory, we have a rigorous quality control process that includes comprehensive testing at every stage of production. Our facilities are equipped with advanced testing equipment, and our quality assurance team ensures that all products meet or exceed industry standards before they are delivered to customers.
How does OMNIC Factory ensure product quality?
Yes, we offer guided tours of the OMNIC Green Factory. Please contact us to schedule a visit and learn more about our sustainable manufacturing practices.
Where are OMNIC Factory’s production facilities located?
OMNIC Factory is located in Italy near Milan and serves OMNIC’s clients across the E.U.. OMNIC also has production facilities in Turkey and Georgia, benefiting our clients in MENA and Asia.
Developing innovative self-service solutions
If you have any queries or require further details, simply fill out the contact form and our specialist will get back to you.
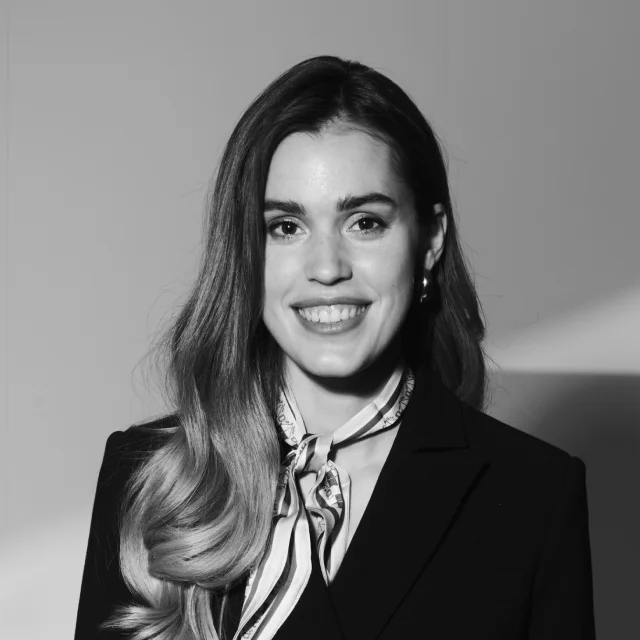
Julia Lockman
Chief Business Developer Officer
Want to cut down operational costs with self-service solutions?
Book a meeting
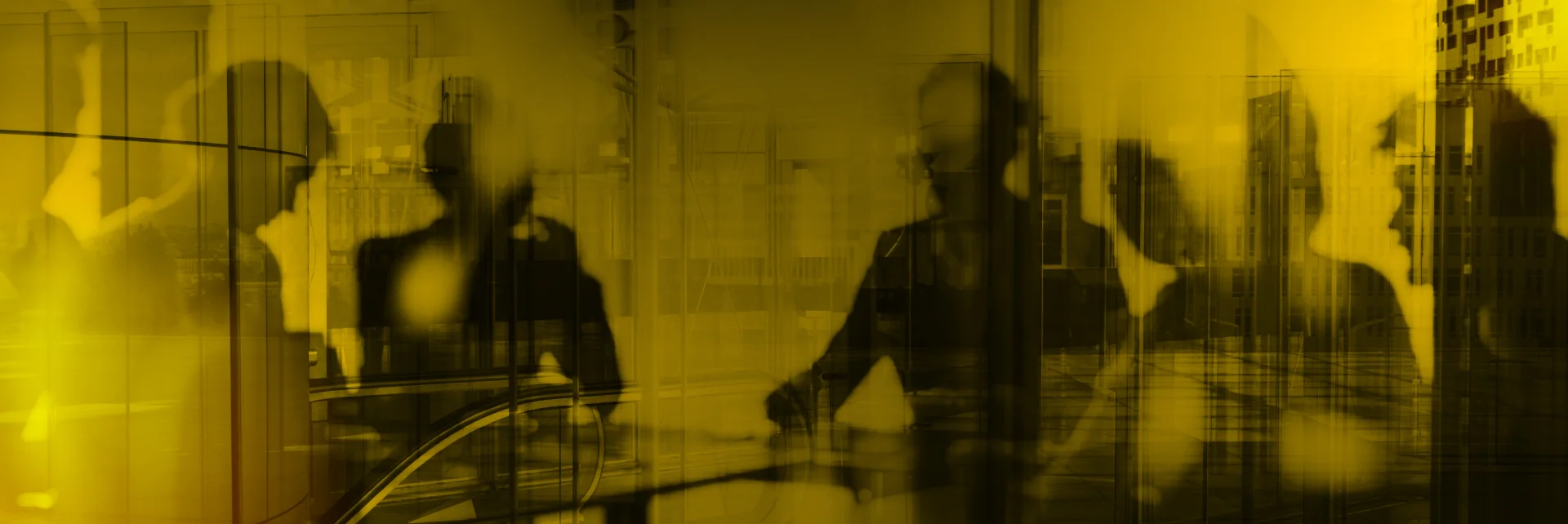